By Mike Rosso
In the previous installment of this column, the interior framing of the new house was getting finished along with the electrical wiring. While this was happening, the first stucco coat was applied to the exterior. I chose a stucco finish for the exterior for a number of reasons. For one, it fits well with the New Mexico territorial style I was after. It is also durable, attractive and weather-resistant.
The process begins with the exterior walls of the home being sheathed in black paper, acting as a barrier between the interior and exterior. The entire area to be stuccoed is then wrapped with a type of galvanized chicken wire for the mud to adhere to. The first, or “scratch” coat of stucco is then applied. We had a family from the San Luis Valley come up and work this stucco magic, and I was lucky enough to be around to watch this technique – one which has been around for centuries. The scratch coat dries dark grey, and a color for the finish coat had to be chosen.
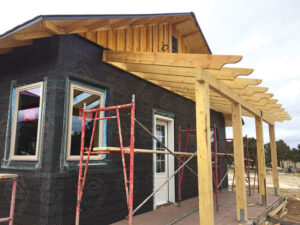
The porch framing is ready for roof sheathing and metal. For the gables at top on the east and west sides, spruce board and batten siding were used to add more architectural flair to the home. Photo by Mike Rosso.
I began walking up to random homes in Salida with a color chart for comparisons. While in Northern New Mexico for a few days I took a good, hard look at the popular stucco colors found there, but in the end I chose a sage green, not common in New Mexico, but being used more and more in Colorado. My friends, Al and Jane in Howard, used this same color on their self-built home, so I visited them to take a closer look and that helped with my final decision. I should also mention that we chose a cement stucco over a synthetic one. Traditional stucco is made from Portland cement, sand, lime and water. Synthetic stucco siding, on the other hand, is multilayered. There is a foam insulation board (typically polystyrene), a coat of the synthetic stucco, fiberglass mesh, and then a top coat. It is flexible and tends not to fade. Traditional stucco is less likely to absorb or be damaged by water and will hold up better to dings, hail and woodpeckers.
Meanwhile, inside the house, the next step was insulation. A fellow named Tex Marshal from Denver was brought in for this task and arrived in his yellow truck to do the job. Insulation performs three major functions; it keeps the house cool in the summer months, warm in the winter months, and limits external noise, which is very helpful in a windy location such as this one.
First, Tex used caulk and expanding foam at the bypass areas; around the windows and doors and any other places where there was the possibility of contact with the exterior, such as plumbing vents and electrical wires. He then attached polyethylene plastic sheeting to the interior walls. For this project, we opted for cellulose, one of the oldest insulation materials on the market. Primarily made of recycled newsprint or denim, it was installed as loose-fill on the attic floor and blown into the interior walls behind the plastic sheeting. Adding insulation to the double-two by-four walls on the north, east and western walls, and to the two-by-six walls on the south, helped create a very well-insulated home. Next month, things start to get very exciting as the drywall goes up and the interior paint begins.